During the initial stage of oil recovery, efforts are usually only able to secure about 10% of a reservoir’s original oil. This is a problem – not just for the oil and gas industry but also for the economy. That’s why most companies have begun using secondary and tertiary oil recovery methods to drive up their oil recovery rate per well.
Although these supplemental methods improve oil production rates, many problems are associated with them. From extensive use of chemicals to becoming less and less effective and everything in between, a better solution to enhanced oil recovery (EOR) has been needed for a long time.
Thankfully, a better solution does exist – and it’s not only more effective than traditional methods but significantly more economically viable as well. That solution is nanobubbles, and it can potentially replace most secondary and tertiary oil recovery methods. But we’re getting ahead of ourselves here…
To learn about the current options available for EOR and how nanobubbles are a better solution, continue reading below. You can also contact Nano Gas™ Environmental to learn more about oil recovery with nanobubbles by clicking the button below.
What is Primary Oil Recovery?
Before you learn about secondary and tertiary oil recovery methods, it helps to understand what happens during the primary recovery process. This can be done in several ways, but the process involves using pressure changes on the well to bring fluids to the surface. Since this is the first stage of recovery, the chosen method almost immediately follows drilling the well shaft.
Regardless of the chosen method, primary efforts usually only recover about 10% of the oil in a well. The pressure used to bring oil to the surface gradually declines, making it challenging (and eventually impossible) to recover further fluids. This is why oil and gas companies utilize secondary and tertiary oil recovery methods – to attempt to access as much of the 90% remaining oil as possible.
What is Secondary Oil Recovery?
Secondary oil recovery is employed when the well’s pressure has dropped too low to continue production. The purpose of this phase is to artificially increase the pressure so oil continues to push upwards to the surface.
Secondary Oil Recovery Methods
Although there are many variations of secondary oil recovery, the most used are waterflooding, gas injection and thermal recovery. Each method has varying levels of efficiency, as well as its own distinct set of benefits and downsides.
Waterflooding
Waterflooding involves drilling a water injection well near the respective oil well, which is then filled with water. The water then flows down into the rock and pushes the oil into the wellbore. Most of the time, this helps to recover an additional 10-15% of the remaining oil.
The benefit is that production rates are increased – and the process doesn’t use harmful chemicals. Unfortunately, the recovery rate remains limited to less than 30% of the well’s total oil capacity, which leaves a significant amount of potential reserves untouched.
The other problem is that, while no harmful chemicals are introduced during the process, waterflooding still presents significant environmental concerns. Since large quantities of water are required, waterflooding contributes to the water scarcity problem. It can also cause channeling, ruining an oil well and rendering it completely useless.
Finally, waterflooding requires someone with an advanced understanding of geology and mathematics. If a mistake is made, the consequences can be severe – and it may be challenging to find someone qualified to perform the waterflooding process.
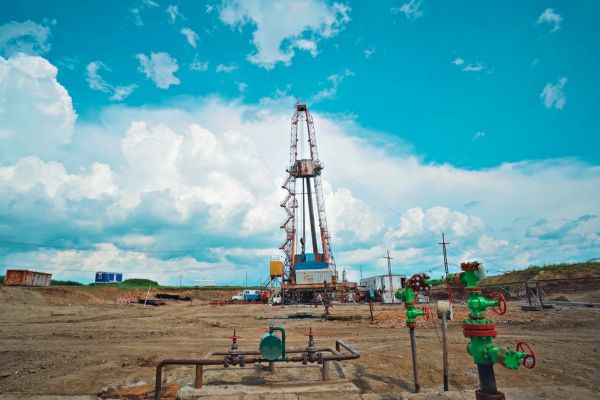
Gas Injection
Gas injection uses a few different gases to reduce the oil’s viscosity and simultaneously increase pressure within the well to help it flow upwards more easily. Carbon dioxide (CO2) is the most used gas, but natural gas and nitrogen are also sometimes used.
This is the most common secondary oil recovery method in the United States. Unfortunately, it’s quite expensive and may not be worth the cost since its effectiveness varies wildly.
While it does increase well recovery, gas injection has several significant drawbacks. Injecting CO2 can cause permanent damage to an oil well, rendering it useless for future production efforts.
Another big downside is that carbon dioxide is highly corrosive. Injecting this popular gas into a well can increase maintenance costs because industrial equipment will suffer unnecessarily excessive wear and tear. Plus, the process has been shown to contribute to climate change when the gas escapes back into the atmosphere.
Thermal Recovery
Thermal recovery relies on steam and fire to improve oil output. Sometimes, this process includes something called “fire flooding.” Fire flooding is a practice that involves igniting a fire inside the well by injecting compressed air nearby.
There are many downsides to thermal recovery. Most notably, the energy requirements are extraordinarily high, and the practice leaves a significant carbon footprint behind. These two facts alone show that thermal recovery is bad for the environment, but there’s an even more pressing problem. This method creates polluted water that’s challenging to clean up, thus contributing to the water scarcity problem.
What is Tertiary Oil Recovery?
Tertiary oil recovery is also known as “enhanced oil recovery” or EOR. Unlike primary and secondary methods, this final phase doesn’t rely on pressure within the well to increase extraction. Instead, tertiary recovery methods rely on changing the properties of the fluids within the well to make them more conducive to extraction. Alternatively, a few methods rely on breaking into the nearby geography to release additional oil reserves trapped in fissures.
Tertiary Oil Recovery Process
There are several tertiary oil recovery methods, the most common of which include hydraulic fracturing or injection of chemicals or gas. Each has varying efficiency rates, along with its unique set of benefits and downsides.
Chemical Injection
As the name implies, chemical injection involves injecting chemicals into an oil well to increase production rates. Several chemicals have been used, but polymers, surfactants and alkalines are among the most popular options. Many oil companies have found success using chemicals to enhance oil production, but this method has a few significant drawbacks.
First and foremost, Economically, chemical injection carries incredibly high costs that most oil and gas companies can’t afford. When they can afford it, the price drives down their return on investment, making it less worthwhile than alternative options.
Next, injecting chemicals into the environment in any capacity can be environmentally devastating. Depending on which chemical is used, the process can pollute water sources, leak toxins into the surrounding ground and harm local flora or fauna.
Hydraulic Fracturing
Hydraulic fracturing, also known as fracking, is a method that involves pumping a fluid containing water, chemicals and small sand particles into the wellbore. The liquid creates significant pressure inside the wellbore, causing cracks and fissures around the current well. Oil is released from these cracks and then brought to the surface.
Fracking is a highly controversial practice because it poses many environmental and safety concerns. For example, fracking has been linked to an increased risk of earthquakes. The process also causes methane gas to leak from the oil well and has the potential to contaminate local water sources.
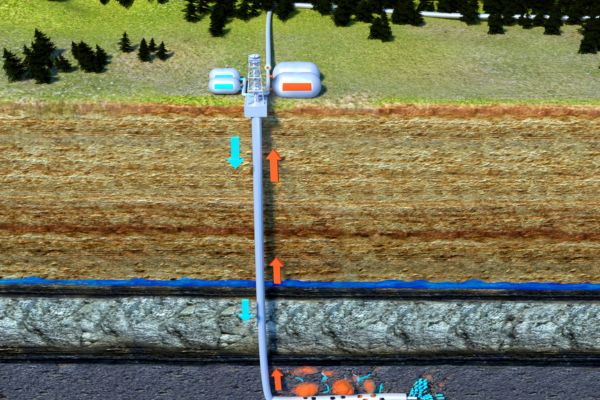
Nanobubbles: A Better Solution
Nanobubbles are a better secondary and tertiary oil recovery method than traditional options. Not only are they more efficient and improve oil recovery rates significantly more, but they also don’t have the many drawbacks associated with alternatives.
How Nanobubbles Work
Nanobubbles are gas-filled bubbles five thousand times smaller than a grain of sand. They’re the main ingredients in the Nitro Nano™ Water used by Nano Gas™ Environmental. To enhance oil recovery rates, nanobubbles are injected into an oil well, which acts as a solvent to decrease the oil’s viscosity, so it rises to the top. Once oil has risen to the top, it can be easily pumped out or scooped off.
But nanobubbles go a step beyond this, too. Since the bubbles are so tiny, they can cling to geology or penetrate the tiniest cracks inside the oil well to kick off the oil, further enhancing production rates. In fact, Nitro Nano™ Water has been shown to increase oil production by 100-150% on average.
Benefits of Nanobubbles for Secondary and Tertiary Oil Recovery
While other EOR methods come with serious drawbacks, nanobubbles don’t. Instead, their usage has many benefits with little to no downsides. For example, nanobubbles are:
- Economically viable
- Highly scalable
- Effective (one oil company saw a 540% production rate increase)
- Environmentally friendly
- Chemical-free
- Produce a very small carbon footprint
- Won’t pollute local water sources
- Doesn’t harm local wildlife or plant life
- Reduces the need for hydraulic fracturing
When you choose Nitro Nano™ Water, you’ll also reap the benefits of fully automated, high-tech equipment with a zero-membrane design to eradicate clogging issues. Nano Gas™ Environmental also provides a comprehensive service that includes everything you need for your EOR efforts, including an expert analysis.
Learn More About Secondary and Tertiary Oil Recovery with Nanobubbles
Nanobubbles are a better solution to enhanced oil recovery that comes with none of the significant downsides associated with alternative options. At Nano Gas™ Environmental, we’re excited to offer a comprehensive EOR service that is more efficient, safer and sustainable.
If your company is interested in our technology, please contact us using the button below. We look forward to discussing how we can help you.